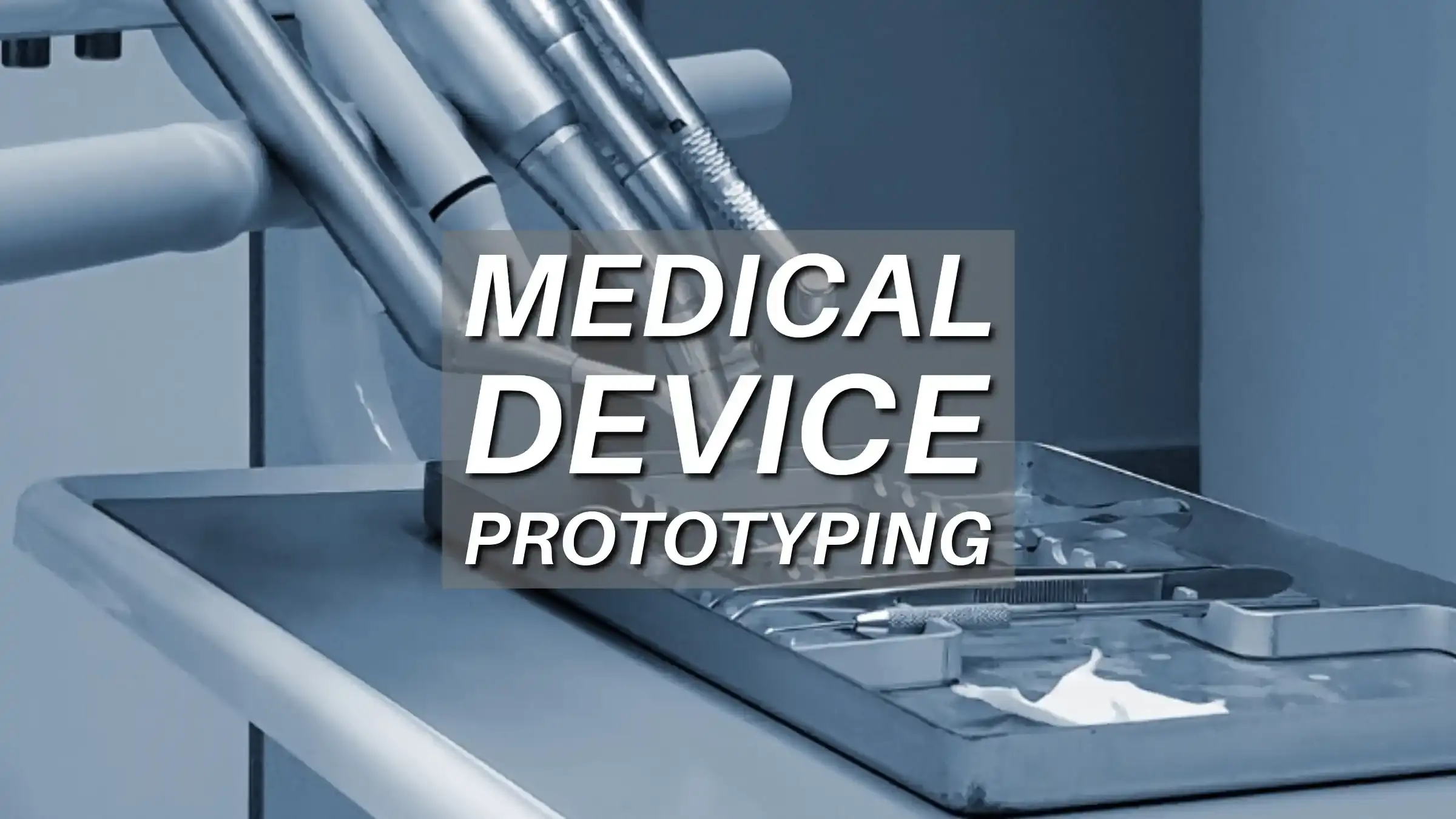
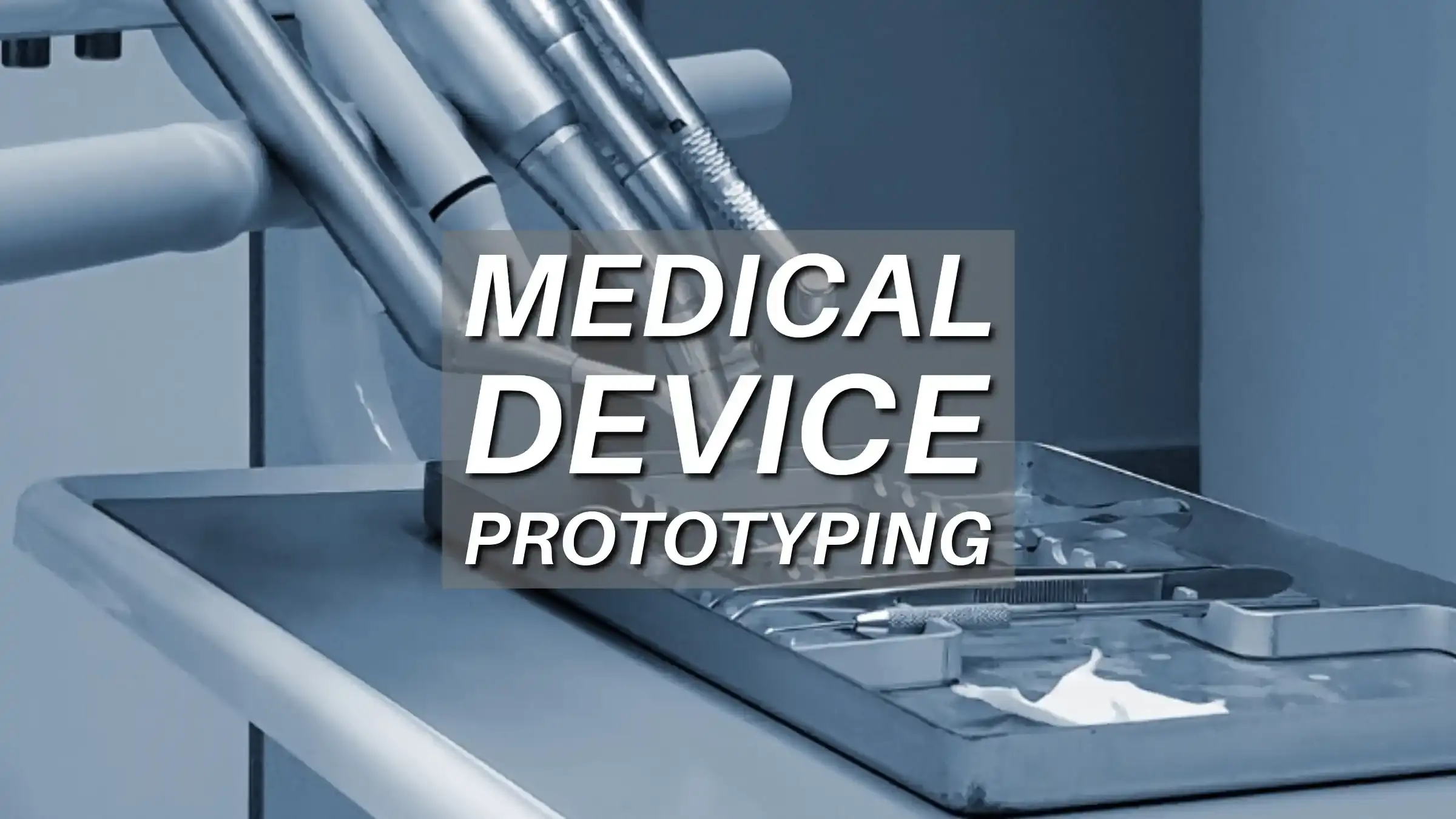
Introduction
Bringing a MedTech product from prototype to mass production is a complex process that requires more than just technical feasibility. Regulatory compliance, cost-efficient design, and scalable manufacturing are critical to success. Without the right strategy, companies risk delays, high costs, and compliance failures.
This guide covers the key steps to ensure a smooth transition from prototype to mass manufacturing while meeting FDA, MDR, and ISO 13485 standards.
1. Optimize Design for Manufacturability (DFM)
A prototype may prove a concept, but mass production requires cost-effective, scalable, and reliable design. Key DFM strategies include:
- Minimizing complex geometries to reduce material waste and machining costs.
- Standardizing components to streamline procurement and reduce supply chain risks.
- Selecting medical-grade materials for durability, compliance, and sterilization.
2. Ensure Early Regulatory Compliance
Regulatory approval is one of the biggest hurdles in MedTech manufacturing. Addressing FDA, MDR, and ISO 13485 requirements in the early stages prevents costly redesigns.
- Use biocompatible and sterilizable materials compliant with ISO 10993.
- Design for IEC 60601 & ISO 14971 safety and risk management standards.
- Maintain detailed design history files for smoother FDA submissions.
3. Conduct Reliability and Durability Testing
Prototypes work in controlled environments, but real-world conditions introduce new challenges. Testing ensures the device can withstand long-term use.
- Accelerated life testing simulates years of wear and tear.
- Environmental stress testing evaluates temperature, humidity, and shock resistance.
- EMC/EMI testing ensures electronic safety and compliance.
4. Build a Resilient Supply Chain
Supply chain failures can derail mass production. Strategic vendor selection and sourcing prevent shortages and delays.
- Partner with FDA-compliant manufacturers for MedTech-grade components.
- Identify secondary suppliers to avoid component obsolescence issues.
- Lock in long-term agreements to stabilize pricing and availability.
5. Scale Assembly & Automation
Hand-assembled prototypes aren’t viable for large-scale manufacturing. Automation and lean production methods improve efficiency and consistency.
- Design for automated PCB assembly and modular construction.
- Implement DFT (Design for Testability) to simplify production testing.
- Use lean manufacturing to reduce costs and improve scalability.
How ITR VN Can Help
At ITR VN, we specialize in MedTech product development, guiding companies from prototyping to mass manufacturing. Our expertise includes:
✅ Electronics & firmware development for scalable manufacturing.
✅ Medical-grade enclosures & PCB design for cost-effective production.
✅ Regulatory consulting to accelerate FDA & CE approvals.
✅ Supply chain management to prevent component shortages.
✅ Production line setup & automation support for efficient scaling.
If you're looking to bring your MedTech device to market with confidence, contact ITR VN today for expert guidance.
ITR – A trusted tech hub in MedTech and Digital Health