Designing Miniaturized, Ultra-Low-Power, and Biocompatible PCBs for Wearable and Implantable MedTech Devices
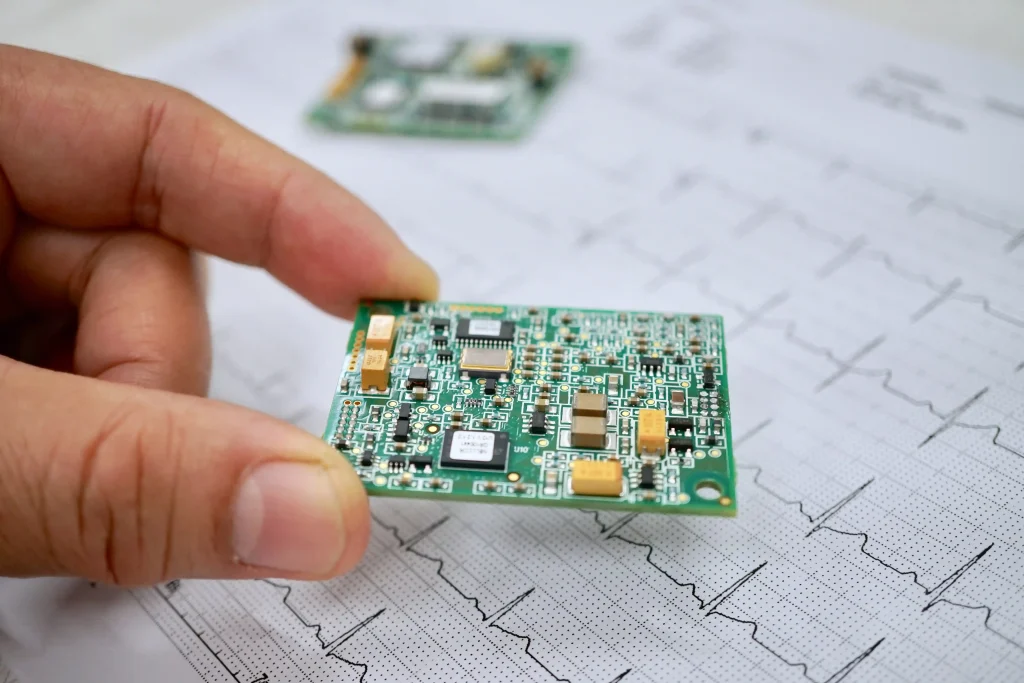
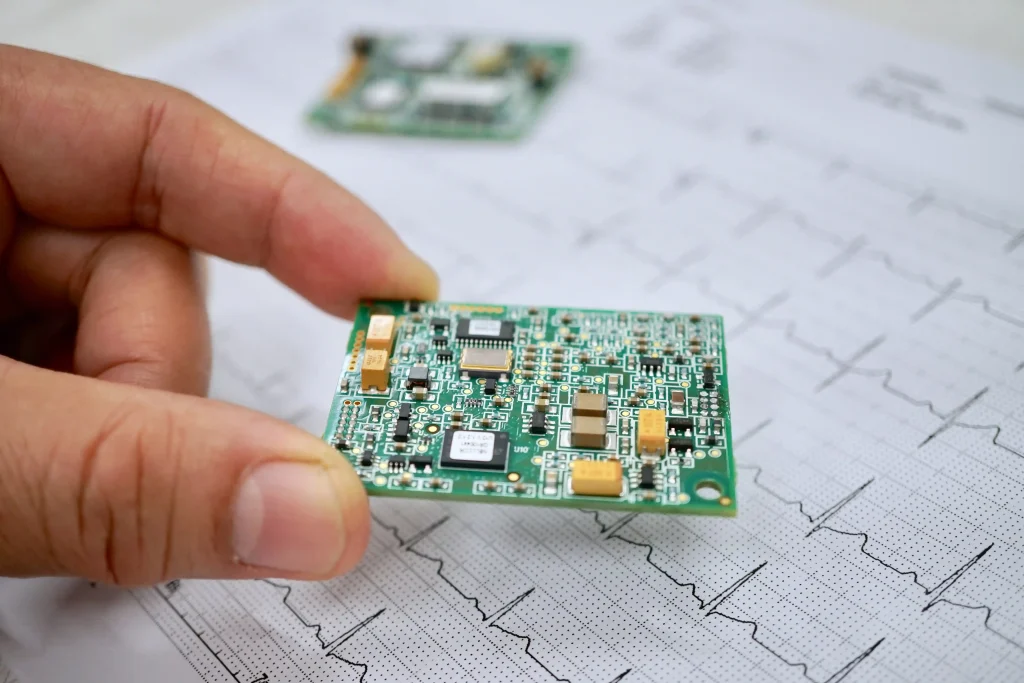
Miniaturized Custom PCB Design
Wearable and implantable medical devices require high-density, miniaturized PCBs to fit within compact enclosures while maintaining signal integrity and power efficiency. Key considerations include:
- HDI (High-Density Interconnect) PCB Design: Enables smaller footprints with fine-pitch components and blind/buried vias.
- Rigid-Flex PCBs: Allow compact form factors with improved durability and flexibility.
- Component Selection: Ultra-small BGA, CSP, and 0201-size passive components optimize board space.
- Electromagnetic Compatibility (EMC) Shielding: Essential to prevent signal interference in miniaturized designs.
Ultra-Low-Power Operation
Medical wearables and implants must operate for weeks or months on a single charge or harvested energy. Optimizing power efficiency involves:
- MCU and SoC Selection: Using ARM Cortex-M or ultra-low-power AI accelerators with deep sleep modes.
- Power Management ICs (PMICs): Efficient DC-DC converters, LDO regulators, and dynamic voltage scaling.
- Energy Harvesting: Leveraging RF, thermal, or motion-based energy sources to supplement battery life.
- Firmware Optimization: Implementing event-driven architectures and aggressive duty cycling.
Wireless Charging Integration
Eliminating physical connectors enhances device longevity, waterproofing, and patient safety. Key wireless charging technologies include:
- Inductive Charging (Qi, WPC): Suitable for wearable patches and low-power implants.
- Resonant Wireless Power Transfer: Allows higher efficiency and distance flexibility for implants.
- Adaptive Charging Algorithms: Optimizes power transfer while minimizing heat dissipation in biocompatible enclosures.
Extreme Biocompatibility & Material Selection
Devices in direct contact with the body must comply with ISO 10993 (Biocompatibility) and USP Class VI standards. Critical materials include:
- Encapsulation & Coating:
- Parylene C (ultrathin, pinhole-free, chemically inert)
- Medical-grade silicone (PDMS) or polyurethane
- PEEK (Polyether ether ketone) for implants
- PCB Substrates:
- Polyimide-based flex PCBs for soft, biocompatible wearables
- Ceramic PCBs (Alumina, AlN) for implantables due to their bio-inertness and heat dissipation properties
- Electrode Materials for Biosensors:
- Platinum, gold, and iridium oxide for ECG, EEG, and bioimpedance sensors
- Carbon-based materials (e.g., graphene, CNTs) for next-gen flexible biosensors
Conclusion
Developing miniaturized, ultra-low-power medical PCBs requires multi-disciplinary expertise in electronics, power management, RF engineering, and biocompatibility. At ITR VN, we help MedTech companies design, optimize, and manage the manufacturing of advanced wearable and implantable devices, ensuring compliance with FDA, ISO 13485, and IEC 60601 standards.
Need expert guidance? Let’s collaborate to bring your next-gen medical device to life.
ITR – A trusted tech hub in MedTech and Digital Health